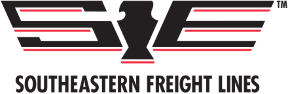
Southeastern Freight Lines, Inc. has a motto: Quality without Question. This simple commitment to the highest quality service has guided the 64 year-old company to more than 380 awards for customer service and excellence. SEFL’s commitment to quality is reflected in numerous company-wide quality control initiatives, one of which now focuses on energy management. A recent software upgrade has enabled the company to effect process changes that have generated significant energy savings.
SEFL pursues a data-driven approach to logistics that “squeezes out” any superfluous steps in transport. Not only has a Statistical Process Control approach been adopted throughout the company, but every employee is trained to maximize efficiency—by the numbers.
SEFL lacked an in-house system to check utility rates and track energy spending, and there was no system in place to maintain historical energy data for auditing or M&V. Duke Drinkard, Energy Consultant for SEFL, was tasked with monitoring all energy invoices, as well as designing retrofit projects. But without a central system for collecting and analyzing the data, accurate data gathering was nearly impossible.
SEFL desperately needed to get a handle on the energy use for their 83 facilities. Since each of the facilities paid their own invoices, tracking overall use and cost was inconsistent. What’s more, many of the facilities did not have trained energy personnel familiar with power and water systems, which meant the invoices that were entered were not necessarily accurate. Drinkard knew that SEFL needed a way for all energy related invoices to be checked by someone who spoke the language of energy management.
SEFL needed a software solution that was simple, reliable and quick.
Prior to using EnergyCAP UtilityManagement, each of SEFL’s 81 regional hubs was approving their own utility invoices. Now, all of the invoices are routed directly to the corporate office and are funneled to one person, who uses EnergyCAP UtilityManagement’s database to capture the valuable energy data. The major benefit to this process is that trained SEFL staff can now review the charges and usage against the history of the account before the invoice is paid, providing a much-needed opportunity to spot problems before bills are paid, saving time and money.
A key piece of the invoicing success was simply achieving consistency. Since different utility bill line items related to energy varied by region, and vendors would sometimes change the names of the various charges on the invoice, Drinkard needed someone who could recognize these changes to help standardize the invoice terminology.
By centralizing the process and training staff to understand the terminologies used for invoicing for the various tracked commodities, SEFL was able to get better reporting on the line item costs that they could control. This has enabled the company to make internal corrections to the way they are using their utilities:
Late Fees: Moving all invoice processing to one location enabled SEFL to nearly eliminate late fees, saving between $20,000 and $30,000 a year.
Error Correction: Drinkard says, “By finding the errors before the invoice is paid, we were able to reduce the time that it takes to make payment corrections by greatly reducing the time it takes to place calls, send letters, and gather supporting documents to the utility companies.”
Energy tracking has also enabled SEFL to detect and address usage anomalies. Drinkard found a water leak that was reported as being fixed. Both the repair person and a local supervisor stated that they had found the problem and fixed it, but the water use continued to increase, rising 10 times higher than the expected amount. Simply by reviewing the invoice history as part of the utility bill approval process, SEFL personnel was able to determine that the leak still needed attention.
Drinkard and SEFL Energy Coordinator Melissa Halsey are constantly finding savings opportunities just by having the data at their fingertips. In one instance, SEFL was able to identify a mysterious water leak. The building had been purchased after an unused restroom had been walled off, and no one even knew it existed. A water line to the toilet started to leak, but there was no visible sign of damage since water ran right into a floor drain. However, when Drinkard noticed a steady increase in the water use recorded on utility invoices, he was able to locate the leak and block off the water supply to the unseen restroom.
But the savings after fixing the leak weren’t as high as Drinkard anticipated, and so he kept looking. Eventually, SEFL discovered that a security guard was routinely allowing another company to fill a 7,000 gallon water tanker twice every weekend from a Southeastern Freight Lines water line at the same site. The abuse had been taking place for at least as long as SEFL had been using EnergyCAP UtilityManagement (four years).The abuse was interrupted and appropriate measures were taken to address and correct the issue.
While using their software to track energy associated with a retrofit project, Drinkard discovered that a facility was being invoiced for more than three times the anticipated electric usage. Drinkard performed an engineering analysis of the equipment to verify the invoicing error.
As it turned out, the electric meter for the facility was giving bad readings. The fix saved SEFL enough in the next two months to pay for their EnergyCAP software in full, and SEFL also received a $78,000 refund from the power company. The refund would have been more, but the state of Tennessee limits the amount of time consumers may contest past invoices to three years.
SEFL has completed more than 20 retrofit projects since 2008, and while some did not return a substantial ROI, others have resulted in dramatic savings, paying for themselves in a little over a year. Drinkard has used EnergyCAP UtilityManagement to evaluate the true ROI of retrofitting projects. While retrofitting companies often touted a 50–60 percent savings as a result of their projects, Drinkard has found that very few have lived up to the hype. Instead, most of the projects have returned a savings between 20 and 22 percent.
SEFL is using EnergyCAP UtilityManagement to monitor energy usage for more than 100 buildings, evaluate return on investment from retrofit projects, and uncover instances of costly waste, saving tens of thousands of dollars. By simplifying the invoice handling process to reduce errors and inconsistencies, and then comparing the expected costs with the actual numbers, Drinkard and Halsey are helping to fulfill SEFL’s commitment to quality and efficiency in the area of energy management.
In the near future, some of the older roofs in the SEFL portfolio will be upgraded by applying an energy efficient coating. There are a number of options available for such a project, and the plan is to use EnergyCAP UtilityManagement to help determine the resultant savings. If the project is a success, the project scope will be broadened to include more of the SEFL building portfolio.
AFL transforms its sustainability by automating utility data management, identifying inefficiencies, and implementing energy-saving projects, resulting in $304,000 in annual savings, enhanced transparency, and strengthened sustainability credentials.
University of Texas Medical Branch (UTMB) identifies savings and builds a case for funding using utility bill, real-time, and carbon emissions data from EnergyCAP.
You cannot manage what you do not monitor; Ark Energy improves M&V audit accuracy and identification of over 7% in energy savings on a client retrofit project using EnergyCAP SmartAnalytics.